Order And Cleanliness In The Workplace
Firstly, order and cleanliness in the workplace are essential when looking for operational efficiency, especially in times of Covid-19. For this reason, in this post we talk about Order and cleanliness in the workplace.
Call us now and get your free quote!
- The 5S method, devised in Japan more than 6 decades ago, continues to help maintain cleanliness and order in the workplace.
- Both components (cleanliness and tidiness) are also essential today, as they prevent contagion.
Also, in the workplace, when there is disorder, dirt or other unnecessary elements, inefficiencies emerge in the processes in the form of lost time, delays, damage and even the risk of accidents.

The 5s methodology, what does it consist of?
In the fisrt place, the 5s methodology includes five key points that anyone should pay attention to in order to keep a workplace in perfect condition.

1. Seiri: Separate Unnecessary Elements
The first “S” translates from Japanese as “separate unnecessary items”. In addition, to do this, we must identify the necessary elements in the workplace.
In addition, once this is done, separate them from the unnecessary ones, eliminating all those that are not essential.
2. Seiton: Placing necessary elements
The second “S” promotes that, once you have the necessary elements in the workstation and have filtered out the unnecessary ones, it is time to place them in an orderly fashion. Also, to achieve this, a series of steps must be followed:
- Decide on the location of each element (as close as possible to the place where each one will be used).
- Set up the means to position each one (furniture, shelves, etc.).
- Mark the place assigned for each element (it is very typical to see the tool boxes with the silhouette of each one).
- Mark on the tool the place that corresponds to it (in a certain drawer or shelf).
3. Seiso: Remove dirt and grime
The third “S” invites you to keep the workstation and tools tidy and clean, which promotes the working environment and helps to reduce defects or accidents, and to maintain an optimal quality level.
4. Seiketsu: Signaling anomalies
The fourth “S” advocates avoiding dirt and disorder through standardization, also, staff training and visual management, and improving tidiness and cleanliness operations.
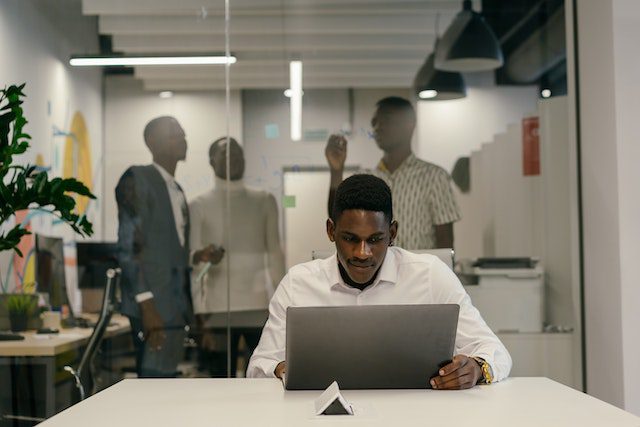
5. Finally, Shitsuke: Keep improving
Finally, the fifth “S” proposes the continuous improvement of the system, also, so typical of Toyota’s work methodologies. In the end, it is a matter of applying the previous cycle over and over again to keep refining and never stop working on this facet.
Finally, hire an effective cleaning service with trained personnel.
Quick Cleaning is the service you need. Contact us and we will give you a free quote!
Call us at: 1-773-800-2524
Don’t think twice and hire the Best cleaning service in Chicago